|
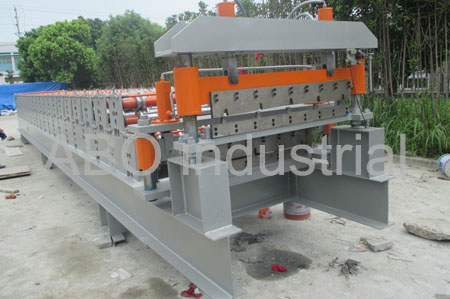 Steel roof sheet double layer roll forming machine
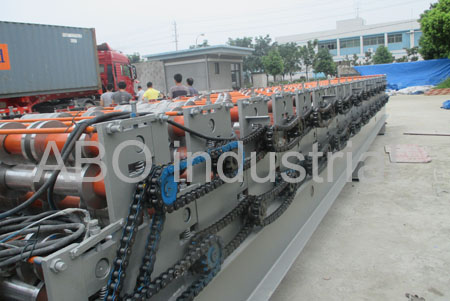 Cold roll forming machine
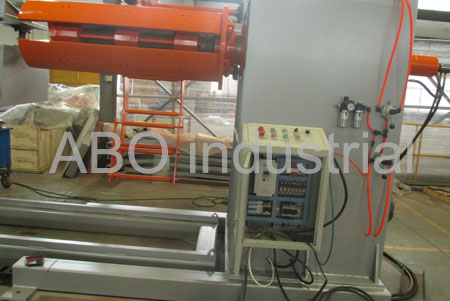 Double layer roll forming machine
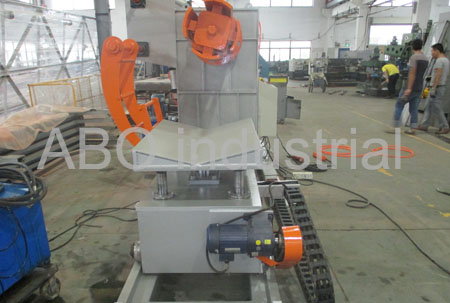 Double layer roof panel cold roll forming machine
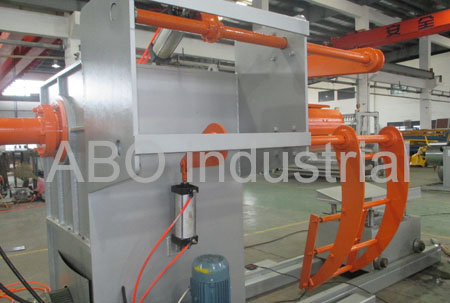 Roof panel double layer roll forming machine
 Metal sheet double layer roll forming machine
Profile drawing
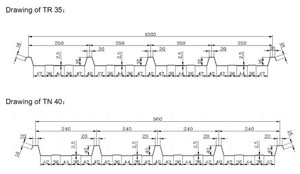
Description of double layer roll forming machine
Double Layer Roll Forming Machine can separate produce corrugated roof and IBR roof in one line or similar two profiles. Automatically cut to length, PLC control, alternating Current Frequency Conversion. This line consists of un-coiler, guiding and feeding device, DUAL LEVEL roll former, run out table, PLC controller, hydraulic post-cutting equipment, electrical control system, hydraulic system, etc.
Application
The products are widely used in building the steel-structure large-scale warehouse, plants, supermarkets, shopping malls, trade markets, stadiums, holiday villages, sanatoriums, hotels, villas, residences, and different kinds of greenhouses.
Advantage
The double layer roll forming machine is available for two profiles roof panel shared one frame, save the cost. Double layer roll forming machine
1) Used to produce different roof panels and wall panels
2) Produced panels have such advantages as below: a) Fine profile b) Attractive color c) Agile connecting d) Slightly curved
3) dual-level roll forming machine
4) We can design and manufacture different type of it to hit your particular profiles
Main technical parameters
General specification
1). Thickness of steel: 0.3-1.0mm
2). Material: PPGI, GI
3). Max. Input width (coil width): 1250mm
4). Total length (from un-coiler to output table): about 15-16M
5). Total weight: about 8T
6). Tolerance of length: 10±2mm
7). Transporting: 1*40ft+1*20ft Container
Main roll forming machine
1). Machine stand: 350H steel welding structure
2). Guide feed way: side sliding type
3). Structure: wall panel, thickness 14mm
4). Number of stations: 18 and 16 stations
5). Main shaft material: 45# steel, O.D.: 70mm, quenching and tempering treatment
6). Roller material: high grade 45# steel, quenching 58-60℃, plated chrome on surface 0.05mm
7). Way of drive: by chain
8). Forming speed: 8-10 m/min
9). Main motor power: 5.5kw
10). Power supply: 380V, 50HZ or at buyer’s requirement, 3-Phase
11). Motor is under the mould, which can save space
12). Dimension (L*W*H): 8.2×1.55×1.5m
13). Weight: 3.5T
14). Bearing: Harbin Bearing
Hydraulic cutter
1). Material of blade and mould: Cr12 steel with quenched treatment 58-62℃.
2). Cutting system: adopt advanced hydraulic cutting system, automatic cut after forming no distortion, waste, high safe factor(main motor stops and then cuts).
3). Cutting type: stop machine cutting.
Electrical system
1). Siemens touch screen;
2). Siemens PLC;
3). Measure the length automatically;
4). Count the quantity automatically;
5). Length and quantity is controlled by computer, the machine will cut automatically as reaching the set length, the machine can automatic stop;
6). It is easy to adjust the error of length;
7). Meter count way: rotary encoder;
8). Converter control: 7.5KW.
Hydraulic system
1). YUKEN system, made in China;
2). Power: 3KW;
3). Oil pump of hydraulic station: gear pump;
4). Hydraulic cylinder: 100mm;
5). Structure of cutting: size of hydraulic station 55×65×90mm;
6). 1 set of electro valve;
7). The oil pipe can not be welded type (protective of oil leak), treatment of welding spot of total machine.
Line composition
10T Hydraulic de-coiler with loading trolley;
Double Layer Roll Forming Machine Unit;
Hydraulic Automatic Cutting Unit;
10M Automatic Run Out Table;
PLC Automatic Control Cabinet;
Electrical system;
Hydraulic system.
Technical process
De-coiler→ Feed with guide→ Roll forming→ Hydraulic cutting→ Run-out table→ Control system
|
|